Concrete and mortar are the backbone of modern construction, but their basic mixture of cement, water, and aggregates (like sand) isn’t always enough to meet the demanding requirements of today’s projects. This is where concrete additives come into play. These specialized chemical or mineral substances are added to the mix in small quantities to significantly enhance specific properties like strength, workability, durability, and adhesion. Understanding how these materials work and choosing the right additive is crucial for anyone involved in construction, from precast manufacturers like our typical customer Mark Thompson in the USA, to large-scale developers. This article delves into the world of concrete and mortar additives, explaining what they are, why they’re indispensable, and how they help you achieve superior results in your building projects. Reading on will equip you with the knowledge to make informed decisions about these vital material components.
What Exactly Are Concrete and Mortar Additives?
At its core, concrete is a composite material made from cement (usually Portland cement), aggregate (like sand and gravel), and water. Mortar is similar but typically uses finer sand and is used for bonding masonry units like bricks or blocks. Concrete additives, sometimes called admixtures, are ingredients other than these basic components that are added to the mixture immediately before or during mixing. These aren’t just fillers; they are active chemical or mineral substances designed to modify the properties of the fresh or hardened concrete or mortar.
Think of them as performance enhancers for your mix. They can range from fine powders to liquids, each formulated to target a specific challenge or desired outcome. For instance, some additives reduce the amount of water needed, while others might speed up or slow down the curing process. As a factory specializing in building materials, including components like Aluminium pastes for aerated concrete, we understand the precise impact these additives can have on the final product. They are indispensable tools for tailoring concrete and mortar performance to specific application requirements.
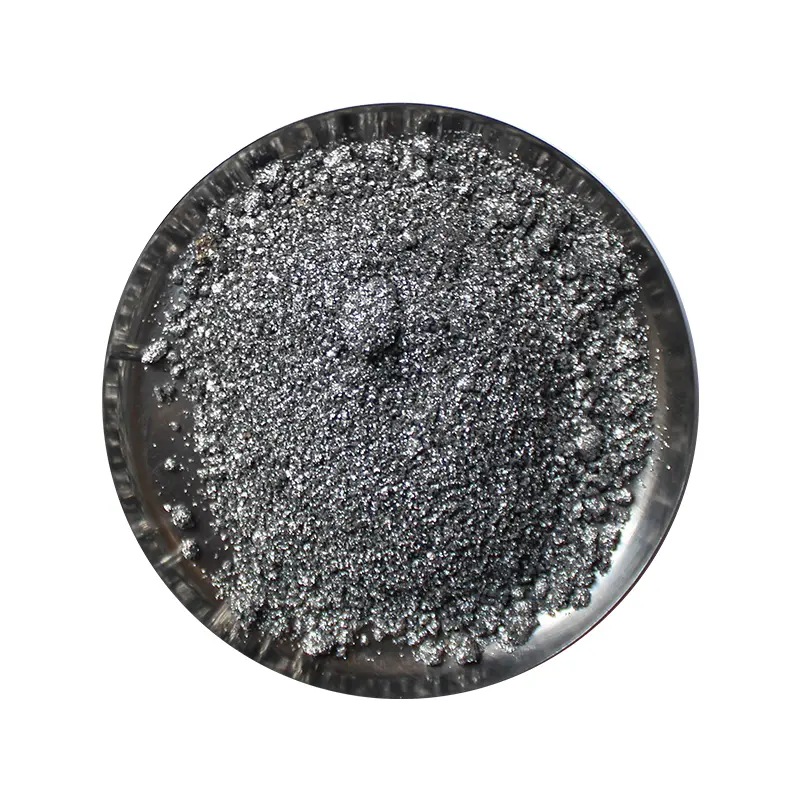
These additives work through various physical or chemical actions. Some affect the hydration process of the cement, influencing setting time and strength development. Others might improve the dispersion of cement particles, leading to better workability and a stronger bond matrix. Mineral additives like fly ash or silica fume can contribute to long-term strength and durability by reacting with byproducts of cement hydration. The key is using the correct additive in the right proportion to achieve the desired result without negative side effects.
Why Should You Add Additives to Your Concrete or Mortar Mix?
The decision to add additives to a concrete or mortar mix stems from the need to overcome limitations of the basic mixture or to meet specific performance criteria required by a project. Standard concrete might be perfectly adequate for some applications, but modern construction often demands more. For instance, pouring concrete in cold weather might require an accelerator to ensure proper curing, while large pours might need retarders to manage heat generation and prevent cracking.
Using additives offers several compelling advantages:
- Improved Performance: Enhance properties like compressive strength, flexural strength, adhesion, resistance to chemicals, and freeze-thaw durability.
- Enhanced Workability: Make the concrete or mortar easier to mix, transport, place, and finish without adding excess water, which would compromise strength. This is crucial for complex formwork or heavily reinforced structural elements.
- Cost Reduction: While additives themselves have a cost, they can lead to overall savings. For example, high-range water reducers (superplasticizers) allow for a lower water–cement ratio, achieving higher strength with less cement, or achieving required workability with less effort. Optimized mixes can also reduce labor costs and speed up construction.
- Durability and Longevity: Certain additives increase the resistance of concrete to environmental aggressors like sulfates, chlorides (from de-icing salts), and carbonation, extending the service life of the structure.
- Specific Applications: Enable specialized applications like self-leveling concrete, lightweight concrete (such as Aerated Autoclaved Concrete – AAC, often used in AAC Block production), or high-strength concrete.
Ultimately, adding additives provides greater control over the concrete or mortar properties, ensuring the final product meets the design specifications and performs reliably under its intended service conditions. It’s about optimizing the mix for performance and efficiency.
How Do Additives Enhance the Compressive Strength of Concrete?
Compressive strength is often the most critical property of concrete. Several types of additives can significantly enhance this key characteristic. The most common way is by reducing the water–cement ratio. Water is essential for cement hydration (the chemical reaction that causes hardening), but excess water creates pores in the hardened concrete, reducing its strength and durability. Water-reducing additives (plasticizers and superplasticizers) allow for a reduction in the required water content (by 10-30% or more for high-range water reducers) while maintaining or even improving workability. This results in a denser, less porous concrete matrix with substantially higher compressive strength.
Mineral additives, also known as supplementary cementitious materials (SCMs), like fly ash, silica fume, and slag cement, also contribute to strength. These materials aren’t inert fillers; they participate in the hydration process over time. Silica fume, with its extremely fine particle size, fills the voids between cement particles and reacts with calcium hydroxide (a byproduct of cement hydration) to form additional calcium silicate hydrate (C-S-H), which is the primary binding agent in concrete. This process not only increases strength but also improves durability and resistance to chemical attack.
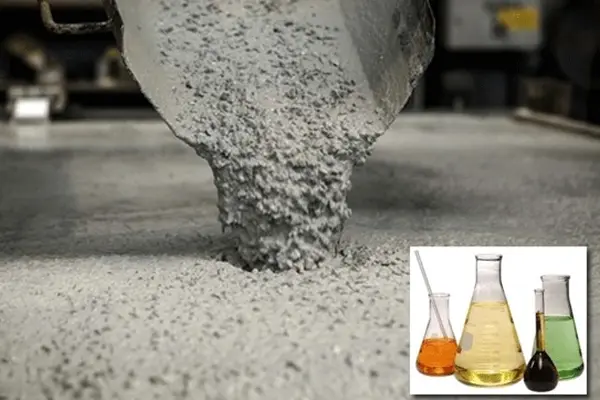
Furthermore, some specialized additives, like certain polymers, can modify the microstructure of the cement paste itself, improving the bond between the paste and the aggregate. While not primarily used for raw strength increase like water reducers, they can contribute to overall toughness and impact resistance. Ensuring consistent quality and dosage of these additives is vital, something we prioritize in our production processes, whether it’s for our aluminum pastes or finished products like ALC Wallboard. Achieving reliable, stronger concrete consistently relies heavily on the correct selection and use of these enhancing additives.
Can Adding Additives Improve Mortar Adhesion Significantly?
Yes, adding additives can significantly improve mortar adhesion, which is crucial for applications like tiling, plastering, rendering, and masonry construction. Adhesion refers to the ability of the mortar to bond strongly to the substrate (like a brick, block, or existing concrete surface) and to any embedded materials (like tiles). Poor adhesion can lead to delamination, cracking, and ultimately, failure of the system.
One key type of additive used to improve adhesion is a polymer modifier, often introduced as a redispersible polymer powder (RDP) or a liquid latex emulsion. When added to the mortar mix, these polymers form a film throughout the mortar matrix as it cures and dries. This polymer film bridges micro-cracks, increases flexibility, reduces water absorption, and, most importantly, creates a stronger mechanical and chemical bond between the mortar and the substrate. This is particularly important for applications on smooth or low-porosity surfaces where traditional mortar might struggle to grip effectively.
Other additives, like cellulose ethers (HPMC), also indirectly contribute to better adhesion. By improving water retention, they ensure that sufficient water remains available for proper cement hydration at the interface between the mortar and the substrate, which is essential for developing a strong bond. They also improve the workability and "stickiness" of the wet mortar, making it easier to apply and ensuring better contact with the surface. Combining these additives allows manufacturers to formulate high-performance tile adhesives, renders, and masonry mortars that provide reliable, long-lasting bond strength.
What Role Does Cellulose (like HPMC) Play as a Mortar Additive?
Cellulose ethers, particularly Hydroxypropyl Methylcellulose (HPMC), are multi-functional additives widely used in dry-mix mortar formulations, such as tile adhesives, plasters, renders, and EIFS (Exterior Insulation and Finish Systems) mortars. Their primary roles revolve around controlling water retention and modifying the rheology (flow behavior) of the fresh mortar, which significantly impacts workability and performance.
The most important function of HPMC is water retention. In thin-layer applications like tile adhesives or plasters applied onto porous substrates, the water in the mortar can be quickly absorbed by the background, leaving insufficient water for the cement to hydrate properly. This leads to poor strength development and weak adhesion. HPMC molecules have a high affinity for water and hold it within the mortar mix, ensuring complete cement hydration even in thin layers or on absorbent surfaces. This controlled water release is crucial for achieving optimal bond strength and preventing shrinkage cracking.
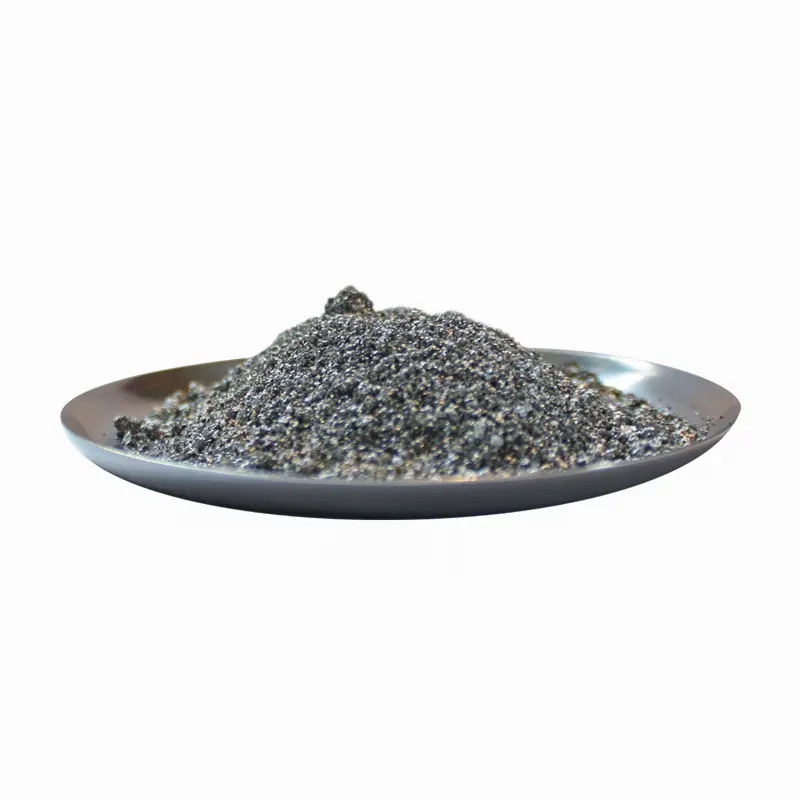
Beyond water retention, HPMC acts as a thickener and improves workability. It imparts a smooth, creamy consistency to the mortar, making it easier to mix and apply with a trowel. It provides good anti-sag properties for vertical applications and improves the "open time" – the period during which the mortar remains workable after application, allowing for adjustments (e.g., positioning tiles). The specific grade and dosage of HPMC can be adjusted to fine-tune these properties, tailoring the mortar product for its intended application, whether it’s for standard masonry or specialized finishes.
How Do Chemical Additives Influence Mixture Workability?
Workability is a crucial property of fresh concrete and mortar, describing the ease with which it can be mixed, placed, consolidated, and finished without segregation (separation of components). Chemical additives play a pivotal role in improving workability, often without the need to add excess water, which would negatively impact strength and durability.
The most common additives for improving workability are water reducers (plasticizers) and high-range water reducers (superplasticizers). These chemical agents work by adsorbing onto the surface of cement particles, imparting a negative charge that causes the particles to repel each other. This dispersion effect breaks up clumps of cement, releasing trapped water and making the mixture flow more easily. This allows for a significant reduction in mixing water while maintaining or increasing slump (a measure of consistency), or alternatively, it allows for a much more fluid mix at the same water–cement ratio, ideal for pumping concrete or filling congested formwork.
Air-entraining agents are another type of chemical additive that influences workability. They introduce billions of tiny, stable air bubbles into the concrete mix. While their primary purpose is often to improve freeze-thaw resistance, these micro-bubbles also act like tiny ball bearings, improving the plasticity and cohesiveness of the mix, reducing bleeding (upward movement of water) and segregation. Other specialized additives like viscosity-modifying agents (VMAs) can also be used, particularly in self-leveling concrete, to enhance flow characteristics while preventing segregation of the aggregates. Proper workability, achieved through the careful use of additives, ensures that the concrete or mortar can be placed correctly, achieving full compaction and maximizing its potential strength and durability.
Are Fiber Additives Beneficial for Structural Reinforcement?
While traditional structural reinforcement in concrete relies on steel bars (rebar), fiber additives offer complementary benefits, particularly in controlling cracking and enhancing toughness. These fibers, typically made from steel, synthetic polymers (like polypropylene or nylon), glass, or natural materials, are mixed directly into the concrete. They don’t usually replace primary structural steel but act as secondary reinforcement, distributed throughout the entire concrete matrix.
The primary benefit of fiber reinforcement is crack control. As concrete cures and dries, it tends to shrink, which can lead to the formation of micro-cracks, especially at early ages (plastic shrinkage cracking). Fibers bridge these potential cracks as they form, restraining their growth and keeping them small. This improves the concrete’s durability and surface appearance. In hardened concrete, if a larger crack does form under load, the fibers spanning the crack provide residual load-carrying capacity, increasing the concrete’s toughness (energy absorption capacity) and resistance to shattering or spalling under impact or seismic loads.
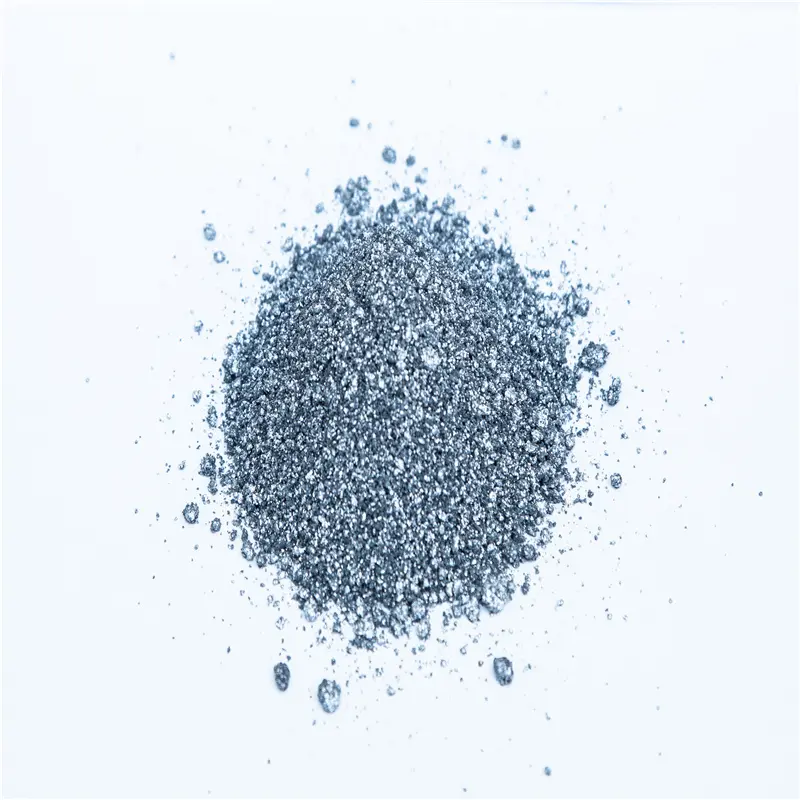
The effectiveness of fiber additives depends on the fiber type, geometry (length, diameter), dosage rate, and proper dispersion within the mix. Synthetic microfibers are excellent for controlling plastic shrinkage, while longer, stronger steel or synthetic macrofibers can provide a degree of post-crack structural contribution, potentially reducing the need for traditional crack-control mesh in applications like slabs-on-ground or precast elements. Adding fiber can sometimes slightly reduce the slump or workability of the mix, which might need to be compensated for with other additives, but the benefits in terms of crack resistance and toughness often make fiber addition a valuable strategy in modern concrete construction.
What is the Impact of Calcium-based Accelerators on Setting Speed?
Setting accelerator additives are used to shorten the setting time of concrete and mortar and/or increase the rate of early strength development. Calcium chloride was historically a common and effective accelerator, but its use is now restricted in reinforced concrete due to its potential to promote corrosion of steel reinforcement. However, other calcium-based and non-chloride accelerators are widely available and used. These additives are particularly useful in specific situations.
The primary application for accelerators is in cold weather concreting. Low temperatures significantly slow down the hydration reaction of cement, delaying setting times and strength gain. This can halt construction schedules and leave the fresh concrete vulnerable to damage from freezing. An accelerator speeds up the hydration process, allowing the concrete to set faster and gain sufficient strength to resist freezing temperatures much earlier. This enables construction work to continue more efficiently during colder months.
Accelerators are also used to speed up production cycles in precast concrete plants or to allow for earlier finishing operations or removal of formwork. By achieving target strengths sooner, manufacturers can turn over casting beds more quickly, increasing production efficiency. Some repair mortars also incorporate accelerators for rapid patching applications where a fast return to service is needed. However, it’s important to use accelerators judiciously, as excessive dosage can lead to overly rapid setting, potential for increased shrinkage cracking, and sometimes a slight reduction in ultimate strength. The correct type and amount of accelerator must be chosen based on the specific project requirements and environmental conditions.
How Do You Correctly Mix Additives into Concrete or Mortar?
The proper introduction and mixing of additives into concrete or mortar is critical to ensure they are uniformly dispersed and perform as intended. Incorrect addition can lead to inconsistent results, localized problems (like fast setting spots or weak areas), and failure to achieve the desired properties. The method of addition often depends on the type of additive (liquid or powder) and the batching process (ready-mix plant or site mixing).
For liquid additives, they are typically added to the mix along with the mixing water or towards the end of the mixing cycle. Many ready-mix plants have automated dispensers that add the precise dosage based on the batch volume. It’s crucial that the additive is mixed thoroughly throughout the batch for a minimum recommended time (often several minutes) to ensure uniform distribution. Adding liquid additives too early or too late, or insufficient mixing, can lead to variability in performance.
Powdered additives, such as pigments, fibers, HPMC, or redispersible polymer powders (often used in dry–mix mortars), require careful handling. They are usually pre-blended with the dry components (cement, sand) before water is added. This helps to prevent clumping and ensures better dispersion. For site-mixed mortar or small concrete batches, powdered additives should be thoroughly blended with the cement and sand first, using a suitable mixer or manual methods, before gradually adding water. Always follow the manufacturer’s specific instructions for dosage and mixing procedure for each additive product, as these are developed to achieve optimal performance and avoid potential issues. Consistent batching and thorough mixing are key to leveraging the full benefits of concrete additives.
Choosing the Right Additive for Your Construction Needs?
Selecting the appropriate concrete or mortar additive depends entirely on the specific requirements of the construction project and the properties you need to enhance or modify. There is no single "best" additive; the choice is driven by the desired outcome, the type of application, environmental conditions, and compatibility with other mix ingredients.
Here’s a simplified thought process:
-
Identify the Goal: What specific property needs improvement?
- Need higher strength or lower permeability? Consider water reducers (plasticizers/superplasticizers) or SCMs (silica fume, fly ash).
- Need better workability without adding water? Use water reducers.
- Need improved adhesion for tiles or plaster? Look at polymer modifiers (RDPs/latex) and cellulose ethers (HPMC).
- Need to prevent cracking (especially early age)? Consider synthetic microfibers. Need toughness? Look at macrofibers (steel or synthetic).
- Pouring in cold weather or need faster setting? Use an accelerator.
- Pouring in hot weather or need more time to place? Use a retarder.
- Need freeze-thaw resistance? Use an air-entraining agent.
- Need better water retention for thin layers? Use cellulose ethers (HPMC).
-
Consider the Application: The end-use influences the choice. An additive suitable for mass concrete might differ from one needed for a tile adhesive or a repair mortar. For specialized products like AAC Block, specific foaming agents (like aluminum paste) and stabilizers are essential, distinct from typical concrete additives.
-
Check Compatibility: Ensure the chosen additive is compatible with the cement type, other additives being used, and aggregates. Some combinations can have unintended negative effects.
-
Follow Specifications and Standards: Adhere to project specifications and relevant building codes (like ASTM or EN standards) regarding the types and dosages of additives permitted.
-
Consult Experts: When in doubt, consult the additive manufacturer’s technical data sheets and seek advice from suppliers or concrete technologists. As a factory, we often work with clients like Mark Thompson to ensure the materials supplied, like our Aluminium pastes for aerated concrete, meet their precise production needs. Making the right choice ensures the concrete or mortar performs as expected, contributing to a successful and durable construction outcome.
Key Takeaways on Concrete and Mortar Additives
To ensure your concrete and mortar mixes perform optimally, remember these key points about additives:
- Purposeful Addition: Additives are specialized chemical or mineral ingredients used to modify and enhance specific properties of concrete and mortar, such as strength, workability, adhesion, and durability.
- Water Reduction is Key: Many additives, especially water reducers (plasticizers/superplasticizers), improve performance by allowing a lower water–cement ratio, leading to stronger, more durable concrete.
- Targeted Benefits: Different additives offer specific advantages: polymers and cellulose (HPMC) boost adhesion and water retention in mortars; fibers control cracking; accelerators speed up setting (crucial in cold weather); air entrainers improve freeze-thaw resistance.
- Correct Mixing is Crucial: Proper dosage and thorough mixing are essential to ensure uniform dispersion and consistent performance of the additive throughout the concrete or mortar mix. Always follow manufacturer guidelines.
- Informed Selection: Choosing the right additive depends on the specific project goals, application type, environmental conditions, and compatibility with other materials. Consider the desired outcome (e.g., increase strength, improve adhesion, improving workability) when selecting.
- Quality Matters: The consistency and quality of the additive itself are vital. Partnering with reliable suppliers ensures the product performs as expected batch after batch.
By understanding and correctly utilizing concrete additives, you can significantly elevate the quality, performance, and efficiency of your construction projects.
Post time: 4 月-15-2025