This article provides a detailed look at Autoclaved Aerated Concrete (AAC) blocks, exploring their advantages and disadvantages for construction professionals. Whether you’re a precast concrete manufacturer, a construction company owner like Mark Thompson from the USA, or a building material distributor, understanding the pros and cons of AAC is crucial for making informed decisions. This guide is worth reading because it offers practical insights based on real-world experience and industry knowledge, helping you determine if AAC is the right choice for your projects. We will also highlight how BTZmoc, a leading factory in China, can meet your AAC needs.
1. What is Aerated Concrete (AAC)?
Aerated concrete, specifically Autoclaved Aerated Concrete (AAC), is a lightweight, precast building material made from a mixture of cement, lime, sand, water, and an expansion agent – typically aluminum powder. This mixture is poured into molds and then undergoes an autoclaving process, where it’s subjected to high pressure and temperature steam. This process creates millions of tiny air pockets, giving AAC its characteristic cellular structure and making it significantly lighter than traditional concrete. AAC can be used for both interior and exterior construction, and it is particularly well-suited for wall panels, floor and roof panels, and blocks.
The key to AAC’s unique properties lies in the chemical reaction between the aluminum powder and the other ingredients during the autoclave process. This reaction generates hydrogen gas, which creates the porous structure that provides AAC with its excellent insulation and lightweight characteristics.
2. What are the Advantages of Using AAC Blocks?
AAC blocks offer a multitude of benefits for construction projects, making them an increasingly popular choice among builders and developers.
-
Lightweight: Due to its porous structure, AAC is significantly lighter than traditional concrete blocks. This lightweight nature reduces the overall load on the structure, allowing for smaller foundations and requiring less steel reinforcement, leading to cost savings. This characteristic is also beneficial for projects where weight is a significant design constraint, such as high-rise buildings. For example, a typical AAC block can be up to three times lighter than a comparable concrete block.
-
Excellent Thermal Insulation: AAC’s air pockets act as excellent insulators. This low thermal conductivity helps maintain a consistent indoor temperature, keeping buildings warm in winter and cool in summer. This thermal efficiency translates to lower energy bills for heating and cooling, making AAC an energy-efficient choice.
-
Fire Resistance: AAC is a highly fire-resistant material. It is non-combustible and can withstand extreme heat for extended periods, providing crucial protection in the event of a fire. This fire resistance makes AAC a safe choice for residential and commercial buildings.
-
Acoustic Insulation: The cellular structure of AAC also provides excellent acoustic protection. It effectively dampens sound transmission, creating a quieter and more comfortable indoor environment.
-
Easy to Work With: AAC blocks are easy to work with. They can be easily cut, drilled, and shaped using standard woodworking tools, simplifying the process of constructing walls and other structural elements. This ease of use saves both time and effort during construction.
-
Cost-Effectiveness: The combination of lightness, faster constrution and reduced need for other materials results in substantial savings.
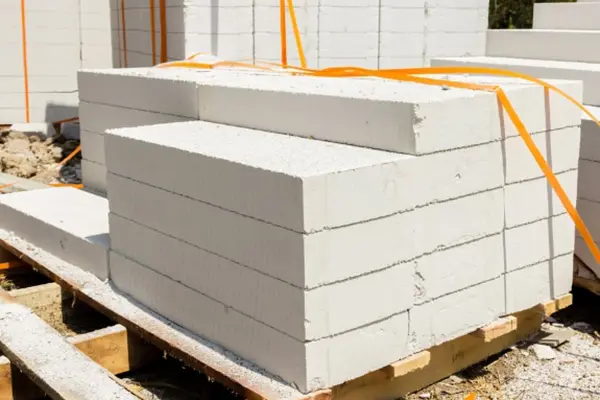
3. What are the Disadvantages of Aerated Concrete?
While AAC offers numerous advantages, it’s important to be aware of its potential drawbacks:
-
Water Absorption: AAC has a relatively high water absorption rate due to its porous structure. While this can be managed with proper sealing and rendering, it’s a crucial consideration, especially in areas with high rainfall or humidity. Excessive moisture can affect the material’s structural integrity and thermal insulation capabilities.
-
Brittleness: Compared to traditional concrete, AAC is more brittle. This means it’s more susceptible to cracking or damage during handling and transportation if not handled carefully. Reinforcement with steel mesh or fibers can mitigate this disadvantage.
-
Lower Compressive Strength: While AAC has sufficient strength for many applications, its compressive strength is generally lower than that of traditional concrete. This may limit its use in load-bearing walls in certain structures, particularly in areas prone to earthquake activity. It is best used in a framed structure.
-
Specialized Mortar: Although it is easy to work with, AAC typically requires a specialized thin-bed mortar for optimal performance. Using the wrong type of mortar can compromise the structural integrity of the wall.
4. How Does AAC Compare to Traditional Building Materials Like Brick and Concrete Blocks?
Compared to traditional building material options like brick and concrete blocks, AAC offers several key differences:
Feature | AAC Blocks | Brick | Concrete Blocks |
---|---|---|---|
Weight | Significantly lighter | Heavier | Heaviest |
Thermal Insulation | Excellent | Moderate | Poor |
Fire Resistance | Excellent | Good | Good |
Acoustic Insulation | Good | Moderate | Moderate |
Workability | Easy to cut and shape | Requires specialized tools for cutting | Requires specialized tools for cutting |
Cost | Generally more cost-effective in the long run due to reduced labor and material needs | Can be more expensive depending on the type of brick and labor costs | Can be less expensive initially, but may require additional insulation for energy efficiency |
Environmental Impact | Eco-friendly, often made with recycled materials | Can have a higher environmental impact due to the energy-intensive firing process | Can have a high environmental impact due to cement production |
As the table shows, AAC blocks offer advantages in terms of weight, thermal and acoustic insulation, and workability. While brick and concrete blocks may have higher compressive strength, AAC’s overall performance and eco-friendliness make it a compelling alternative.
5. What is the Manufacturing Process of Autoclaved Aerated Concrete?
The manufacturing process of AAC involves several key steps:
- Raw Material Preparation: The raw materials for AAC – typically sand (or fly ash), cement, lime, water, and aluminum powder – are precisely measured and mixed.
- Mixing and Casting: The ingredients are thoroughly mixed to create a slurry. This slurry is then poured into molds.
- Rising: The aluminum powder reacts with the other ingredients, generating hydrogen gas. This gas causes the mixture to expand, creating millions of tiny air cells.
- Cutting: Once the mixture has partially hardened, it’s cut into blocks or panels of the desired size.
- Autoclaving: The cut blocks or panels are placed in an autoclave, a large pressure vessel, where they are subjected to high-pressure steam at temperatures around 190°C (374°F) for 8-12 hours. This autoclave hardening ensures better strength, dimensional stability, and durability.
- Packaging and Shipping: After autoclaving, the finished AAC products are cooled, inspected, packaged, and prepared for shipment.
It is important to note that materials for manufacturing autoclave aerated concrete require careful quality control to ensure consistent performance. The particle size distribution of the aluminum powder, for example, is critical for achieving the desired density and pore structure.
6. Is AAC an Eco-Friendly Building Material?
AAC is widely considered an eco-friendly building material for several reasons:
- Resource Efficiency: AAC production often utilizes recycled materials, such as fly ash, a byproduct of coal-fired power plants. This reduces the demand for virgin raw materials and diverts waste from landfills.
- Energy Efficiency: The excellent thermal insulation properties of AAC contribute to reduced energy consumption for heating and cooling buildings, lowering the overall carbon footprint.
- Lower water use: AAC manufacturing requires less water.
- Reduced Waste: The precise manufacturing process of AAC minimizes material waste. Furthermore, AAC itself is recyclable, meaning it can be crushed and reused in new construction.
- Non-Toxic: AAC is made from environmentally clean ingredients and does not release harmful chemicals or gases into the environment.
Overall, the environmental impact of AAC is significantly lower than that of many traditional building materials, making it an eco-friendly choice for sustainable construction. BTZmoc is committed to providing aluminum paste that contributes to this environmental friendliness.
7. What are the Thermal Insulation Properties of AAC?
AAC is renowned for its exceptional thermal insulation capabilities. The millions of tiny air pockets within its structure create a barrier that significantly reduces heat transfer. This low thermal conductivity means that AAC buildings require less energy for heating and cooling, resulting in lower energy bills and reduced carbon emissions.
The thermal performance of AAC is often measured by its R-value, which indicates its resistance to heat flow. Higher R-values represent better insulation. AAC typically has significantly higher R-values compared to traditional concrete or brick, making it an excellent choice for energy-efficient buildings. This characteristic is especially beneficial in climates with extreme temperature variations.
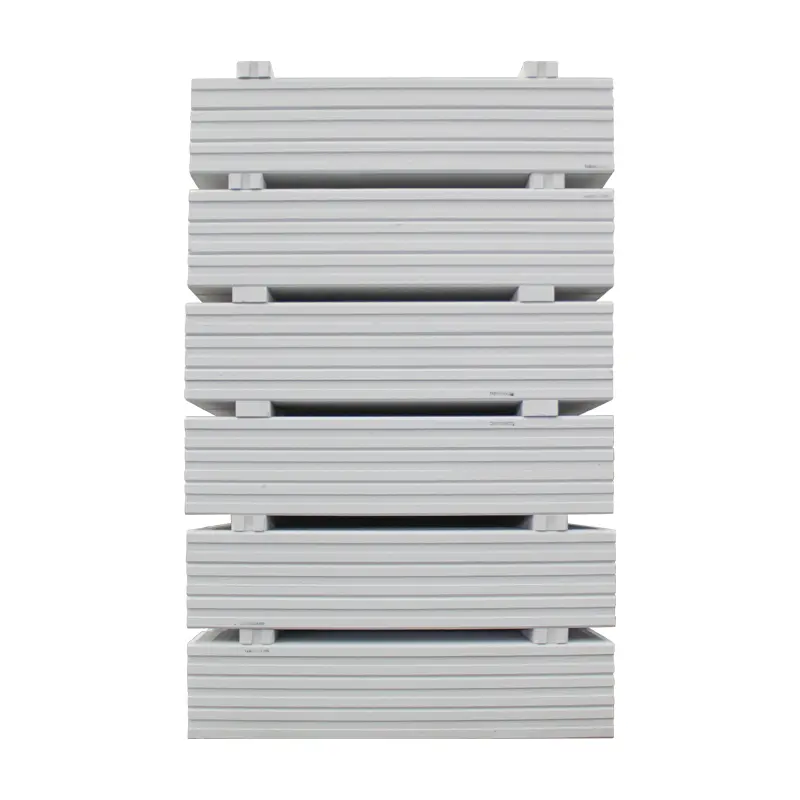
8. How Does AAC Contribute to Acoustic Insulation?
In addition to its thermal properties, AAC also provides excellent acoustic insulation. The porous structure of AAC effectively absorbs sound waves, reducing noise transmission between rooms and from the outside environment.
This acoustic performance is particularly valuable in multi-family dwellings, schools, hospitals, and other buildings where noise control is a priority. AAC’s ability to dampen sound contributes to a quieter and more comfortable indoor environment. The vapor permeability coefficient of AAC is another factor to consider, as it relates to the material’s ability to manage moisture and contribute to a healthy indoor environment.
9. What are the Key Considerations for Purchasing AAC and Aluminum Paste?
For procurement officers like Mark Thompson, several key factors are crucial when purchasing AAC products and aluminum powder:
- Quality Consistency: The quality consistency of aluminum paste (gas generation performance) is paramount for reliable AAC production. Consistent particle size distribution and reactivity are essential.
- Structural Integrity and Dimensional Accuracy: Structural integrity and dimensional accuracy of ALC wallboard and AAC blocks are crucial for ensuring proper fit and performance in construction.
- Certifications: Verify that the AAC products and aluminum powder meet relevant industry standards and building codes. Look for certifications such as ISO standards, building code compliance, and material safety data sheets (MSDS).
- Moisture Content: Check the moisture content of the AAC products to ensure they are within acceptable limits.
- Thermal Conductivity Ratings: Review the thermal conductivity ratings to confirm the insulation performance of the AAC.
- Logistics: Consider the logistics for bulky materials, including transportation costs and delivery schedules.
- Payment Methods: Clarify the available payment methods and terms.
- Supplier Reliability: Choose a reputable supplier with a proven track record, like BTZmoc, to ensure consistent product quality and timely delivery.
Addressing these concerns upfront will help avoid potential pain points such as inefficient communication with supplier sales representatives, shipment delays impacting construction schedules, inconsistencies in the quality of aluminum paste leading to production issues, and damage during transportation of ALC/AAC blocks.
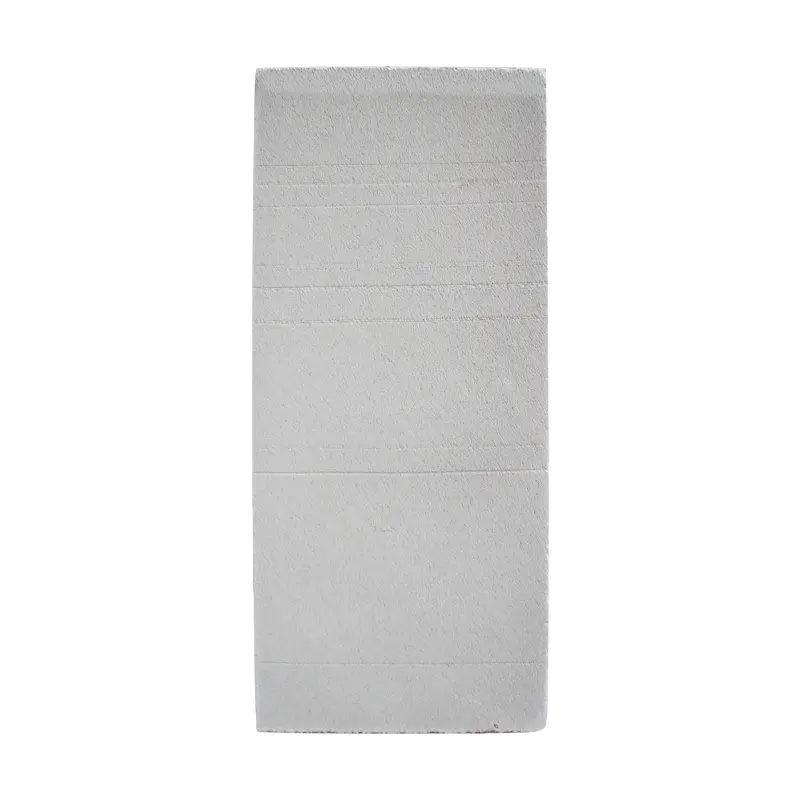
10. How Can BTZmoc Help Meet Your Aerated Concrete Needs?
BTZmoc, a leading factory in China with 7 production lines, specializes in providing high-quality building materials for the aerated concrete industry. We offer:
- Aluminium pastes for aerated concrete: Our aluminum pastes are formulated for optimal gas generation and consistent performance in AAC production. We offer various formulations to meet different AAC density requirements.
- ALC Wallboard: Our ALC wallboards are lightweight yet strong, providing excellent thermal and acoustic insulation. They are dimensionally accurate and easy to install.
- AAC Block: Our AAC blocks are manufactured to the highest standards, ensuring consistent quality and performance. They are fire-resistant, eco-friendly, and compliant with relevant building standards.
We understand the needs of our customers, like Mark Thompson, and are committed to providing:
- Competitive Pricing: We offer cost-effective solutions without compromising on quality.
- Reliable Supply: Our 7 production lines ensure a consistent and reliable supply of products.
- Excellent Customer Service: Our team, including Allen, is dedicated to providing responsive and efficient communication.
- Global Reach: We export to major markets, including the USA, North America, Europe, and Australia.
We actively participate in exhibitions to connect with our customers and showcase our products. We encourage you to contact us to discuss your specific requirements and learn how BTZmoc can be your trusted partner for aerated concrete solutions. Aluminium pastes for aerated concrete are a key component of our offerings, and we also offer finished products like ALC Wallboard. We also take pride in offering the most reliable and consistent AAC Block.
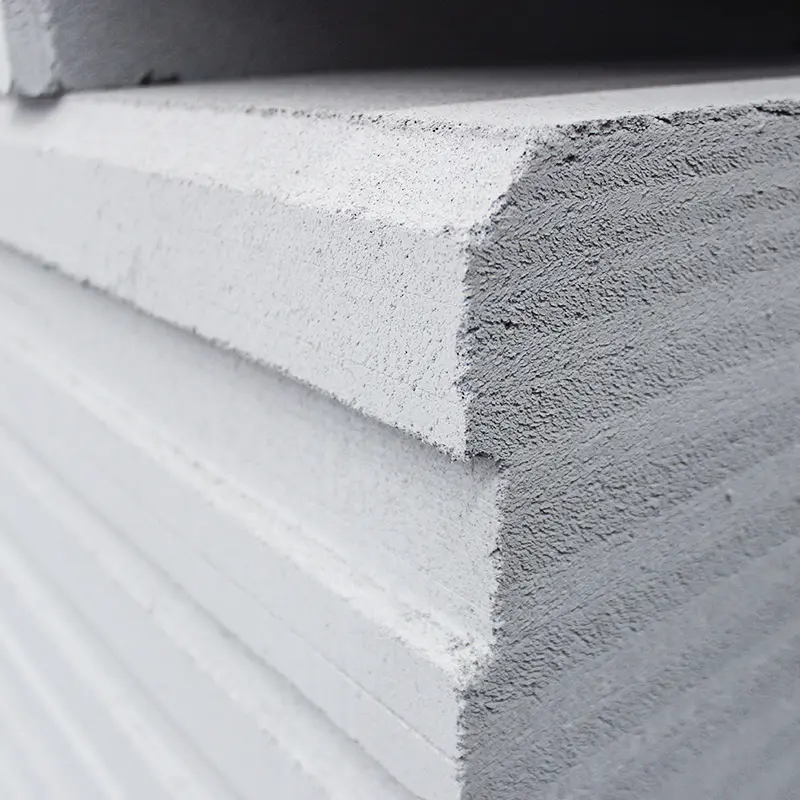
Key Takeaways
- AAC blocks offer significant advantages in terms of weight, thermal and acoustic insulation, fire resistance, and workability.
- The disadvantages of AAC, such as water absorption and brittleness, can be managed with proper handling and construction techniques.
- AAC is an eco-friendly building material due to its resource efficiency, energy efficiency, and recyclability.
- The quality of aluminum paste is crucial for consistent AAC production.
- BTZmoc is a reliable supplier of high-quality aluminum paste, ALC wallboard, and AAC blocks, serving customers globally.
- Choosing a supplier like BTZmoc can help mitigate common purchasing pain points in the construction industry.
- AAC products is an energy-efficient choice.
- The longevity of AAC makes it a sustainable and advantageous choice for the conscientious builder.
Post time: 3 月-25-2025